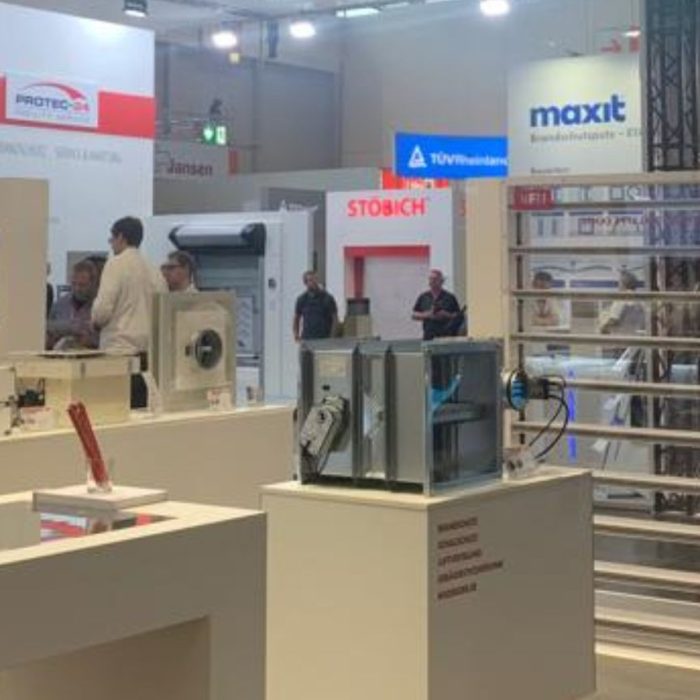
NOVISOL beim FeuerTrutz 2023: Fachaustausch
Fachaustausch NOVISOL beim FeuerTrutz 2023 In unserem Artikel erfahren Sie mehr über die Neuigkeiten...
Erfahren Sie mehr über das neue Deckensystem im Postbahnhof in Baden, das entwickelt wurde, um Korrosionsrisiken bei der Gebäudedämmung zu verhindern.
Erfahren Sie mehr über das neue Deckensystem im Postbahnhof in Baden, das entwickelt wurde, um Korrosionsrisiken bei der Gebäudedämmung zu verhindern.
Erfahren Sie mehr über das neue Deckensystem im Postbahnhof in Baden, das entwickelt wurde, um Korrosionsrisiken bei der Gebäudedämmung zu verhindern.
In der Praxis der Industrie ist das Thema Korrosion unter Isolierungen (CUI) ein äußerst weitreichendes Thema. Das Team von NOVISOL hat die wichtigsten Erkenntnisse neuer Studien für Sie zusammengefasst, damit Sie bei Ihren Bauprojekten und bei der Instandhaltung dieser einen Überblick darüber haben, wie Sie Korrosion vermeiden können. Bei der Isolierung von Gebäuden und Anlagen muss darauf geachtet werden, dass das Korrosionsrisiko maximal minimiert wird, um Folgeschäden zu vermeiden. Dämmungen alleine können keinen hundertprozentigen Schutz davor garantieren, allerdings das Risiko signifikant reduzieren. Erfahren Sie in diesem Artikel mehr darüber, zu welchen Schlüssen unabhängige Studien gekommen sind und welche Materialien die Gefahr von Korrosion deutlich reduzieren.
Betroffene Leitungen Mediantemperaturen zwischen 0 °C und 175 °C Besonders kritisch: über 50 °C | Anlagen im Wechseltemperaturbetrieb Tauwasser durch Temperaturschwankungen Erhöhtes Risiko bei salzhaltiger Luft | Nicht kontinuierlich betriebene Anlagen |
Mittlerweile ist der Zusammenhang zwischen Dämmmaterialien und dem CUI-Risiko in verschiedenen Industrien, vor allem in der Öl- und Gasindustrie, bekannt. Allerdings wird der Einfluss von Dämmstoffen auf das Korrosionsrisiko in internationalen Normen noch nicht vollwertig berücksichtigt. Dementsprechend gibt es aktuell keine standardisierten Testmöglichkeiten, durch welche die Leistungsfähigkeit eines Isolationsmaterials zur Verminderung des CUI-Risikos geprüft werden kann. Allerdings wurde in den Niederlanden ein Testverfahren entwickelt und geprüft. Dieses Testverfahren wurde von dem Institut TNO-ENDURES für den Gaskonzern Shell entwickelt und ist mittlerweile in der gesamten Öl- und Gasindustrie anerkannt.
Bei diesem standardisierten Test wurden die Dämmmaterialien des Herstellers Armaflex bewusst unterschiedlichen Situationen ausgesetzt, die zu einer Korrosion führen. Im Fall A wurde eine unlegierte Stahlleitung mit einer durchschnittlichen Temperatur von 80 °C mit warmem Salzwasser besprüht. Dadurch wurde in beiden Fällen sichergestellt, dass Wasser in die Isolierung eindringen konnte und dadurch ideale Bedingungen für eine Korrosion gegeben sind. Anschließend wurden beide Szenarien für 6 Monate getestet. Bei dem Testverfahren wurden bewusst Korrosionsprozesse ausgelöst, damit im Extremfall einer Korrosion die Qualität des Dämmmaterials, in diesem Fall Armaflex, getestet werden kann.
Eine Hälfte der Leitung wurde mit einer doppelten Lage von Armaflex Platte (Dämmschicht jeweils 25 mm) isoliert. Es wurden mehrere Löcher um die gesamte Isolierstärke gebohrt, um den Schadensmodus zu simulieren. Wie erwartet kam es nach dem Testzeitraum von 6 Monaten zu Korrosionen, allerdings nur in direkter Umgebung der Bohrlöcher. Die komplette Unterseite des Rohres und alle anderen Bereiche der Leitung blieben vor Korrosion geschützt.
Bei Fall B wurde die andere Hälfe der Leitung exakt gleich präpariert und zusätzlich mit einem glasfaserverstärkten Kunststoff als Wetterbarriere ummantelt. Es wurde bewusst nur die Ummantelung durchbohrt, damit der Dämmstoff unbeschadet blieb. Nach dem Test fühlte sich zwar die äußere Dämmschicht feucht an, allerdings war die innere Isolationslage vollkommen trocken. Es wurde auf der gesamten Stahlleitung keine Korrosion festgestellt. Durch dieses Testszenario konnte nachgewiesen werden, dass durch die Armaflex-Isolierung das Eindringen von Feuchtigkeit an der Oberfläche der Leitungen verhindert werden konnte.
Um nachweislich zu prüfen, welche Dämmmaterialien in welchem Ausmass das Korrosionsrisiko unter der Isolierung minimieren, gab Armacell weitere Korrosionsprüfungen bei dem spezialisierten Institut InnCoa (Neustadt/Donau) in Auftrag. Alle Dämmsysteme wurden fachgerecht auf Stahlleitungen angebracht und hoher Luftfeuchtigkeit in einer Klimakammer ausgesetzt. In jedem Testkörper wurde ein Loch mit einem Durchmesser von 5mm Breite und mit 10 mm Tiefe durch die Ummantelung in die Isolierung gestanzt, damit das Eindringen der Feuchtigkeit in die Dämmung garantiert werden konnte. Diese wurden in einer Reihenkonfiguration mit Luftzirkulation implementiert und Temperaturbedingungen von 35 °C ausgesetzt. Es wurde sichergestellt, dass die Luft in der Kammer zirkulierte und die relative Luftfeuchtigkeit betrug 80 %. Das in den Rohren in einer Endlosschleife zirkulierende Wasser betrug eine Temperatur zwischen 5 °C und 80 °C. Der kontrollierte Testzeitraum betrug 65 Tage.
Abschliessend wurden die Dämmsysteme und die Oberflächen nach ISO 10289 klassifiziert, dem Verfahren zur Korrosionsprüfung von metallischen und anorganischen Überzügen auf den metallischen Materialien. Der Schutzgrad RP misst den Grad des Schutzes der Oberflächen vor Korrosion. Bei einem RP von 10 ist das beste Ergebnis und bedeutet, dass 0 % der Oberfläche Korrosion aufweist.
Fachaustausch NOVISOL beim FeuerTrutz 2023 In unserem Artikel erfahren Sie mehr über die Neuigkeiten...
Schallschutz, Privatsphäre & Sichtschutz Trennwandsysteme: Beispiele aus der Praxis Erfahren Sie jetzt mehr über...
Ein Überblick Brandschutzdecken Erfahren Sie jetzt mehr über die zertifizierten Brandschutzlösungen von NOVISOL. Ein...
Wir sind Ihr verlässlicher Partner und vorkonfektionieren Ihre Blechformteile in einer Spitzenqualität und zu einem fairen Preis. Wir freuen uns darauf, Sie als Werkstattpartner begrüssen zu dürfen und auf die Zusammenarbeit.
Montag | 07:30 — 12:00 / 13:00 — 17:00 |
Dienstag | 07:30 — 12:00 / 13:00 — 17:00 |
Mittwoch | 07:30 — 12:00 / 13:00 — 17:00 |
Donnerstag | 07:30 — 12:00 / 13:00 — 17:00 |
Freitag | 07:30 — 12:00 / 13:00 — 16:30 |
Wir sind Ihr verlässlicher Partner und vorkonfektionieren Ihre Blechformteile in einer Spitzenqualität und zu einem fairen Preis. Wir freuen uns darauf, Sie als Werkstattpartner begrüssen zu dürfen und auf die Zusammenarbeit.
Montag | 07:30 — 12:00 / 13:00 — 17:00 |
Dienstag | 07:30 — 12:00 / 13:00 — 17:00 |
Mittwoch | 07:30 — 12:00 / 13:00 — 17:00 |
Donnerstag | 07:30 — 12:00 / 13:00 — 17:00 |
Freitag | 07:30 — 12:00 / 13:00 — 16:30 |